The Technical Support department of INTRACOM DEFENSE provides integrated services of technical support, maintenance and training throughout the period of performed projects and for each produced product and system, available to company’s customers, focusing to the quality, efficiency and fast reaction:
- Warranty and Maintenance of Products and Systems
- System Installation
- Managing of Repair Parts
- Customer ‘s Training
- Technical support and Consulting services
- Analysis, Validation, Design, Testing and Reliability Control.
Warranty and Maintenance of Products and Systems
- Preventive maintenance
- Corrective maintenance
- Subsystems repair
Managing of Repair Parts
Based on the repair and maintenance historical data of the delivered products and systems, the Technical Support Department maintains stock of critical spare parts, in order to minimize the time-to-repair and to achieve the maximum operational availability of the customer’s equipment. Long Lead and obsolete parts are also included in the stock management procedures.
Customer’s Training
- Training for project operation and usage of products
- Practical On the Job training
- Maintenance Training (1st and 2nd level)
Technical Support and Consulting Services
- Studies of feasibility and technical studies
- Analysis and evaluation of field equipment and laboratory data
- Development of maintenance capabilities and resources
Analysis, Validation, Design, Testing and Reliability Control
- Models, allocations and estimates of reliability (MIL-HDBK-217F)
- Analysis of damage, effects and criticality (FMECA)
- Selection of materials and application instructions (Derating Guidelines)
- Testing of Accelerated Life product and Reliability Verification
- Testing of environmental stress (ESS)
Specialized personnel
- Engineers of studies
- Technicians of Repair (laboratory and field)
- Technicians of field (ground systems, vehicle, tank and ships)
- Electronic Engineers of Design and Development
- Trainers of handling and maintenance of all scales
- Over 40% of the staff are graduated in Technological and University institutions
Skilled technicians are trained in accordance with international standards of soldering and joints (ANSI-J-STD-001C, IPC 610 A, IPC 7711 – 7721).
Facilities
- Area 1000 m 2 of Controlled Access
- Special area for storage classified material
- Contemporary control instruments
- Completely equipped repair stations
- Special testing devices (Testers)
- Contemporary tool equipment
- Technical Bibliography
- Files of repair parts
- Vehicles for transporting the personnel and the necessary equipment in the field
Certified Center for repairing Cards
Procedures for repairing cards (PCB / PBAs) in accordance with international standards (J-STD-001 / IPC-7711 / IPC-7721)
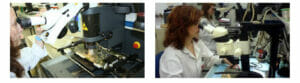
Service Provisions
Maintenance and Repairs
- Maintenance and repair of units
- Flexible repair procedures
- Direct time of restitution
- Certified Repair
- Preventive and scheduled maintenance
- Field support
- Mobile equipment for repair on the field
- Troubleshooting with peripherals devices
- On time intervension and availability of service team
- Help Desk
- Direct customer support
- Provision information in special technical requests.
- Management of repair parts
- Central Management through integrated system MRP
- Direct information for the availability of materials
- Order of not available materials with high priority
- Management of customer’s repair parts
- Management of obsolete parts
System Installations
The Technical Support Department of INTRACOM DEFENSE maintains a team of specialized and adequately trained technicians to perform mechanical, electrical and electronics installations of complex systems onto military vehicles (wheeled and trucked), ships and submarines as well as to ground fix facilities.
The installation are delivered as “Turn Key” managing all the project phases including package, shipment, modification/preparation of supporting hardware, installation of equipment, racks and cabling, power supply, functional setup and conduction of final acceptance tests.
- Autopsy of the facilities and recording customer’s requirements
- Study and preparation to ensure the interconnection with the existing infrastructure
- Organization and planning
- Supervision and implementation
- Activation and Certification
- Controls of Acceptance
- Extended support during the operation
Design and Implementation of Specialized Units
- Recording of operational and environmental requirements of customer
- Study of Feasibility – Proposals of Optimization
- Design, construction and certification of prototype
- Serial production of final product
- Modification – Upgrading of existing systems
- Reverse Engineering – redesign units
Examples of Design and Implementation of Specialized Units
- High pressure system leak check
- Control system leak tissue submarine S209
- Measuring brake torque motor Radar Antenna Y / N
- Printed Circuit Design up to 24 Levels
Formal maintenance procedure- Repair
- Delivery of the material and documents from customer
- Material Identification
- Recording data of the material in ERP system
- Optical control of the incoming materials
- Recording data of the process in the database
- Repair Inspection (technical support, equipment, materials) Repair Investigation (expertise, equipment, materials)
- Repair and Functional Test
- Issue reports and certificates
- Failure Analysis Report (FAR)
- Inspection/repair Report (IRR)
- Acceptance Test Report (ATR)
- Certificate of Conformity (CoC)